The sophistication of coal storage keeps increasing. Once considered dirty and environmentally hazardous, structures are now built with tight emissions control, minimal to zero product interaction with the outside world and innovative utilization of byproducts that used to be destined for landfills. Coal is a resilient industry that keeps adapting to stay relevant.
Even as the industry sees proactive change, a few things remain the same, and one of these is that domes are well suited for coal storage. To help coal companies plan the ideal project, Dome Technology relies on this simple rule of thumb: The type of coal determines the reclaim, and the type of reclaim determines the dome shape.
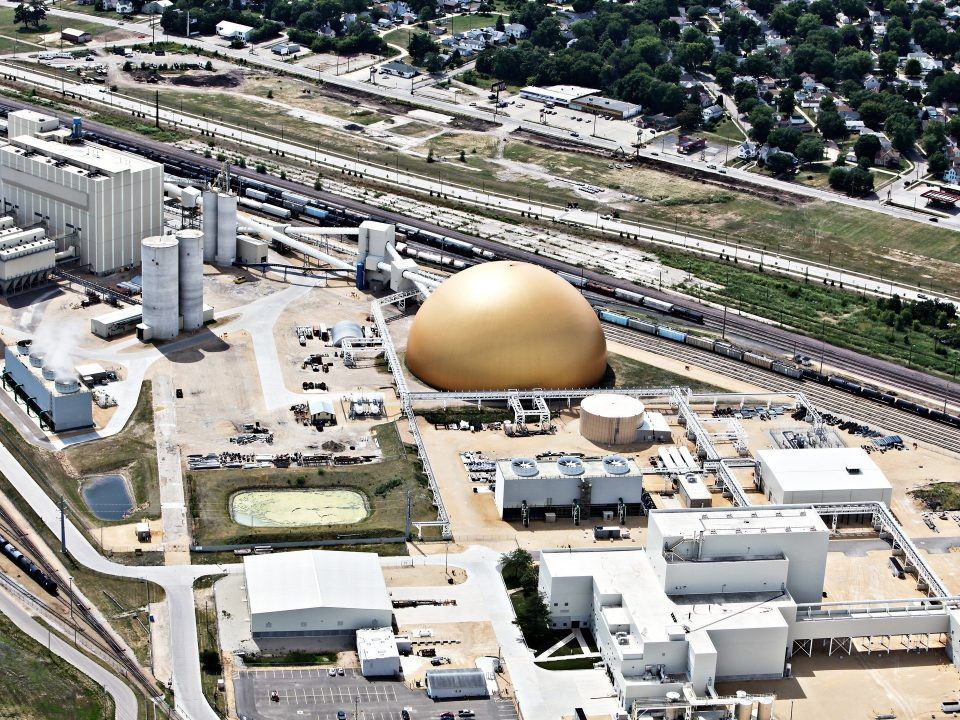
Coal types and reclaim options
With subbituminous coal, storage and handling requirements are stringent. Based on volatility, coal companies must decide how they’ll maintain access to the pile for handling potential fires and hot spots. A doughnut-shaped pile is a good option for storing subbituminous coal. The pile is placed and reclaimed using a stacker reclaimer; this model allows access to the pile and can work particularly well when the cleanout happens every couple weeks. A monitoring system on the inbound conveyor is another must so hot coal is rejected before being placed in the storage. Fugitive dust cleanup is also essential to proper storage and avoidance of fire and explosion concerns.
A kidney-shaped pile can also work well. The stacker creates a pile that tapers off on the side, and the filling arm’s swing is 230 to 250 degrees. This shape provides ample access to the pile, so while it might not make the most of a dome’s capacity, it does provide peace of mind and safety when managing and monitoring a volatile product.
With bituminous and lignite coal, stacking and reclaim options are expansive. From front-end loader to stacker reclaimer or drag chain, coal producers can be choosy, balancing low cost with sophistication. Dome Technology’s team has also seen rotary plows with cone-shaped piles as an effective reclaim option, and another effective choice is tall domes with a live-bottom floor to keep product rotating.
Reclaim options and complementary dome types
For a reclaim system to work best, the dome must be built to complement it. Subbituminous storage is safest within a hemispherical dome with easier hot-spot access from the inside of the storage, but the inside shape of the dome must be engineered accurately too. For instance, with a stacker reclaimer, the shell is built to account for the reclaim arm being fully extended without scraping the dome wall. Typically, the dome is built with a short stem wall and a pedestal upon which the stacker reclaimer sits.
This model can leave pockets of product behind on the floor, so the dome floor is often built with a slope to ensure product can be mostly reclaimed to the tunnel hopper instead of building up in hard-to-reach spaces.
Bituminous, anthracite or lignite coal all benefit from stacker or live reclaim. When a 100-percent live reclaim system is selected, the dome can be taller and smaller in diameter—an ideal model for sites with less construction space. If a stacker is selected, a hemispheric dome with a short stem walls is recommended.
Every coal dome is customized so reclaim and dome type work hand in hand. For one potential customer working with bituminous coal, Dome Technology recommended four tall domes with 80 percent live reclaim that feeds three below-grade tunnels and affords the ability to clean out the rest with front-end loaders. With these domes holding 60,000 metric tons apiece, the company could achieve its intended goal of moving 4 million tons a year, or about 76,000 tons a week, all thanks to a solid plan at the front end.
“Once we know the type of coal, that will push the type of reclaim, which will push the dome shape, and then we design it to fit it on the site if possible,” sales manager Lane Roberts said.
Dust control: The benefits of a sealed envelope
A reinforced-concrete storage dome is a natural choice for companies eager to minimize environmental impact. Dust is a concern with many stored products, but it can’t escape a monolithic concrete dome since joints or seams don’t exist. Inside, the truss-free interior discourages dust build up, and a host of dust-control systems exist in the marketplace to manage dust production. Automatic dust-collection systems can be designed to convey dust back into the product stream.
Sealed and seamless, a dome keeps product inside and prevents interaction with the environment. This envelope is multi-layered; a dome is built using the shotcrete method, so concrete is sprayed in place without any construction joints. On the exterior, a high-strength PVC membrane covers the entire structure. Between the membrane and the concrete, urethane foam protects the life of the structure as well as the stored product.
The PVC membrane ensures complete waterproof protection for the reinforced concrete shell and, consequently, the material stored within. A mold-resistant UV-protective resin coats both sides of the membrane, providing long-term protection from these two common sources of degradation. No other silo option offers this type of waterproof protection, and this exterior requires almost zero superficial maintenance.
Domes are always built without rivets, fasteners or mechanical connections found in other storage, thus eliminating potential sources for leaks and rust. This comprehensive approach to waterproofing promises long-lasting protection for stored product and the structure itself.
The double curvature of a dome provides strength at all points of the structure, even near the apex. With strength at the top, a coal company has no problem securing adequate space for dust-collection systems.
Structural strength
The dome itself can survive a disaster other types of storage might not and will likely reward companies with insurance-premium savings. A dome has inherent strength other bulk-storage structures do not. Should an earthquake, tsunami, hurricane or tornado occur, the structure has a better chance of survival than a traditional building.
In a deflagration event, a dome’s round shape channels energy out with less structural damage. Historically, square and rectangular explosion venting has been the norm in storing products prone to deflagration, but Dome Technology’s team has pioneered a round hybrid model that began to be installed on projects in 2016. Whether a pre-manufactured rectangular panel or a metal cladding piece, a squared-off panel creates a weak spot. Round panels are preferable because there are no sharp corners for stress concentration in the structure. This allows for a release of pressure, protecting the structure.
The proprietary explosion vents are comprised of a circular geodesic steel lattice covered with the same PVC fabric used in the dome construction process. The panel is anchored to the dome with explosion-venting relief screws that remain secure during the design dead, live and wind loads. But in the event of a deflagration event, the screws release the panel and allow for the release of the excessive internal pressure. The system is watertight and meets the required operational design loads.
When an explosion occurs, the fabric accepts the load and transfers it uniformly around the ring’s circumference. “Because it’s circular we can predict the load going to each of the fasteners really well,” said Jason South, Dome Technology Vice President of Engineering, Research, and Development. “If it were rectangular, the pressure going to each fastener could be different,” and more difficult to estimate.
Each explosion vent is unique to the project. Dome Technology’s engineering team uses discrete finite element modeling and computational fluid dynamics to model the potential explosion event and determine the amount of open area required for the blast panels such that the pressure only gets to a certain level before fasteners release.
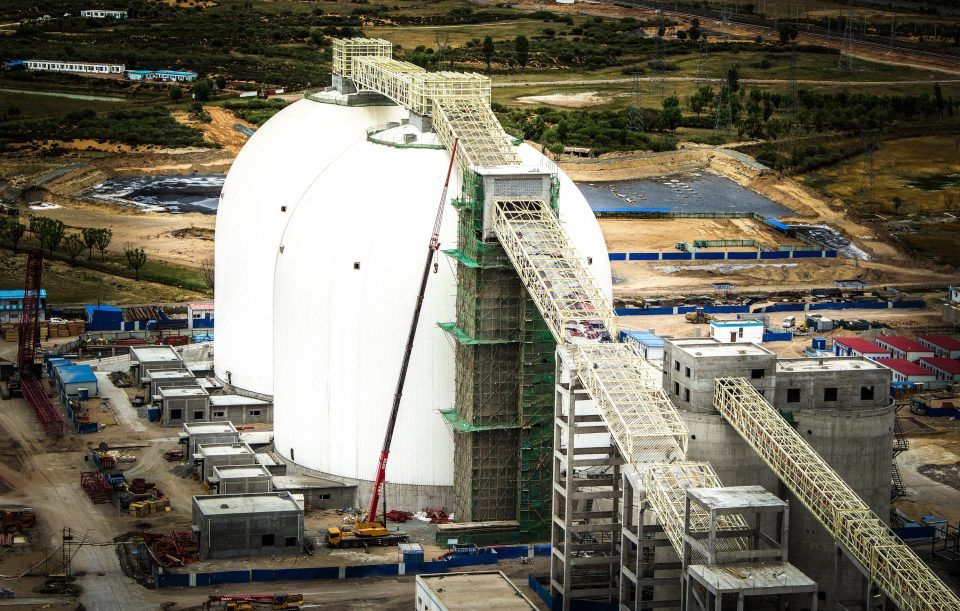
Lessons from China Coal
When Dome Technology CEO Bradley Bateman met with China Coal management, it was clear what the company wanted: a high live-reclaim system at an economical price—and good looks didn’t hurt either.
China Coal sought storage facilities for both its Hulusu and Menkeqing coal mines, located fifteen miles apart in north China’s Inner Mongolia province. Based on “their ability to keep out outside moisture,” Bateman said a series of domes was a more economical solution than traditional silos. And in the land of the yurt, another factor “was the aesthetics; it was the way they look,” he said.
Dust buildup is always a concern with coal storage, and China Coal took it seriously. Since domes are built without the use of interior supports, dust build-up on trusses isn’t a concern. Secondary explosions—the kind caused when initial explosions shake loose accumulated coal dust—are less likely because the support-free domes have no ledges for dust to build up. “One of the major dome advantages is to prevent fire because there are no interior shelves to collect dust, and China Coal liked that a lot—for them it was a big deal,” Bateman said.
Other design features are key to fire prevention. To render the pile of coal inert, China Coal can seal the domes at top and bottom to cut off oxygen sources and pump nitrogen inside to lower the oxygen level. With a thermal scanner over the belt on the inbound receiving side, infrared cameras check temperatures on coal, while on the belt, to make sure no off-spec product enters the dome. A linear heat cable monitors for fire on the belt, also examining bearings in case one is throwing sparks; this cable might detect a fire travelling along the belt length before it reaches the thermal scanner. A product unique to combustion-prone materials, this system shuts down conveyance and alerts facility management of the fire. Depending on the setup, workers can either extinguish the fire, or an existing fire-suppression system takes care of the problem.
Today visitors to one mine will see three domes housing 60,000 metric tons of coal apiece and in the distance three identical domes at the other mine. An innovative material-handling system gives China Coal the ability to move product fast. Inside each dome, a full hopper system similar to a series of funnels situated side by side allows coal to flow through the structure under its own weight rather than by loader.
Other design details also add value, especially since the possibility of coal self-igniting in the dome was one of China Coal’s main concerns, said Zhao Jiapeng of China Coal. The exterior PVC membrane prevents moisture from contributing to spontaneous combustion. Secondary explosions are less likely because the domes have no ledges for dust to build up. China Coal can also render the pile of coal inert by sealing the dome and pumping nitrogen to lower the oxygen level.
The project wrapped in August 2015, a true joint effort between China Coal and Dome Technology. “The achievement from the Menkeqing and Hulusu projects belongs to both of our corporations,” Zhao said.
Dome Technology’s domes allow companies to build storage that meets green regulations now and into the future. The dome is an out-of-the-box, customized solution for companies hoping to grow business while acting as a better steward of the environment.
By Rebecca Long Pyper for Dome Technology
Editor’s note: This article was published in the third issue of World Coal 2021.