St Marys Cement, part of the North American operations of global building materials supplier Votorantim Cimentos, knew that to efficiently move and sell product, they needed to make the nearby water work for them.
The company’s plant in Charlevoix, Michigan, included a DomeSiloTM by Dome Technology designed to store 70,000 metric tons—good news except for one thing: Once Lake Michigan froze over, there was no way to move product to customers further south. And in such a frigid climate, that could mean waiting months at time.
St Marys Cement (St Marys) already operated a transload facility in Chicago but lacked the capacity to store additional volume that could be sent from Charlevoix and elsewhere. So the company bulked up their storage space by adding a DomeSilo to the Chicago site, a cost-competitive alternative to silos and flat storage that would make enough product available to last through the winter.
“We were looking for additional storage capacity and an economical solution; domes provide both,” said Randy Pryor, plant manager for St Marys’ Charlevoix plant.
In Chicago, St Marys fills the dome with as much as 50,000 metric tons of cement, making issues like freezing lakes and insufficient storage a thing of the past.
“Now St Marys can fill the Chicago dome in the fall, and it gives them enough cement powder in the winter to provide better customer service, even when the lake freezes over and they can’t get the barge down there,” Dome Technology operations manager Brent Hardy said.
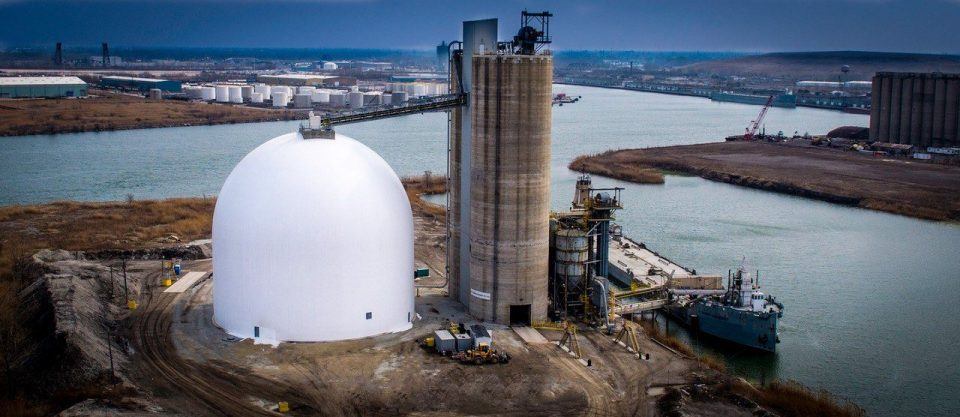
Making the most of portside property
Transporting bulk storage via water isn’t just an efficient way to ship; it has become a viable way for companies to expand business operations from one city to the next rather than having to buy land adjacent to existing plants.
But portside property comes at a premium, and companies get less land for their money than they might elsewhere. A DomeSilo makes the most of available property, providing more storage than silos or flat storage with the same size footprint.
Because of its height, a dome allows companies to stack product deeper, taking up less property at the site. The increased capacity is made possible by geometry: The double curvature of a dome lends itself to the ability to build up, rather than out, and the curve provides strength at all points of the structure, even at the apex. The entire interior of a dome, then, can be used to contain product.
A dome’s strength and geometry also provide a tolerance for differential settlement. Those qualities combined with geotechnical engineering and site analysis ensure proper foundation selection and performance.
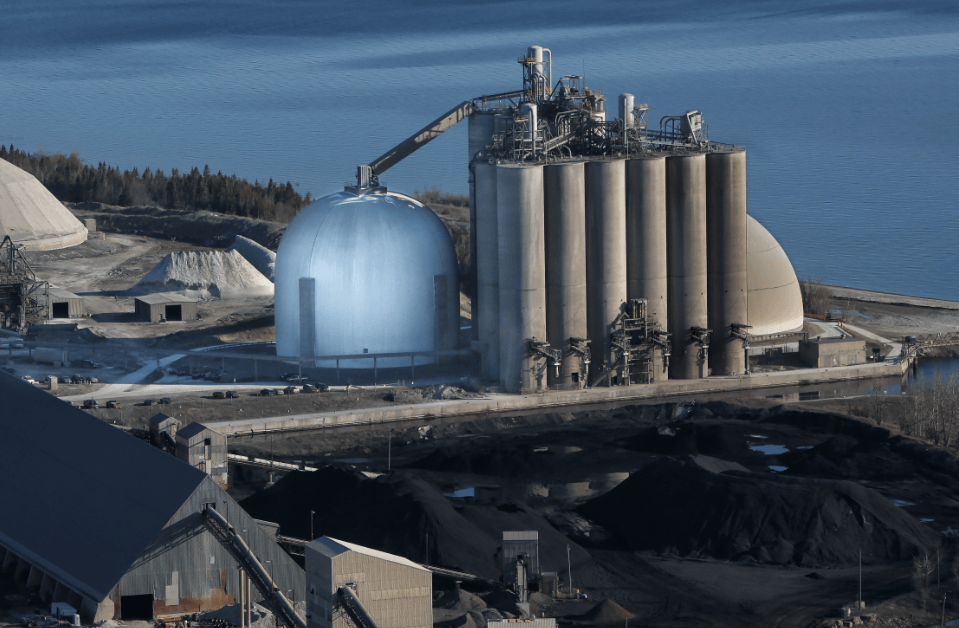
Foundation considerations
Another issue with building on a port is wet or compromised soils. The Dome Technology team specializes in innovative alternatives to expensive deep foundations; some common options include the following:
- Where the top six to eight feet of ground is less-than-desirable material, crews replace it with controlled structural fill. This model allows for some settlement, but the amount will be within tolerable parameters for a dome.
- When the top 15 to 50 feet of soil is questionable, stone columns are a workable option. Crews use an auger to remove earth in about a 30-inch diameter hole until a more stable, soil-bearing layer is reached. Rock then fills the hole and is compacted, even laterally so the soil around it is supportive. With soft or clay-concentrated soils, a casing must be added to the hole to prevent it from collapsing on itself.
- With a dome, a ringbeam can provide a shallow foundation alternative at sites with acceptable soil conditions. This is an especially viable option at sites with consolidated soils from supporting heavy storage facilities in the past.
For areas where deeper foundations are required, other systems are available:
- In a piled-raft system, steel or precast concrete piles are driven into the ground. A layer of crushed rock three feet thick is placed on top, along with a fabric geogrid, which stiffens the rock mat and adequately strengthens the soil for the structure to be built on top.
- Piles are driven and topped with a heavily reinforced concrete pad three to four feet thick; in this model, the system is designed to bear on those piles, so the structure is essentially supported by stilts although built at ground level.
- Soil mixing is an option when soil is questionable for as much as 30 feet of depth. An auger is used to mix the soil with cement and lime; the mixture is then compacted. For similar soil conditions, stone columns often cost less and can be installed faster.
- In sites with high water tables, a six-inch-wide piece of plastic called a wick drain provides a way for water to escape in areas of low permeability. A wick drain is driven vertically into the ground to the desired depth, and water flows to this strip, which acts as a channel to remove excess water. Consolidation of this soil can usually be expected within about three months with a surcharge loading.
- Dynamic compaction requires the use of a crane; a heavy weight is lifted and dropped repeatedly to densify soil. Vibration and horizontal pressure make this a poor option for structures being built very close to a sea wall, and some soils don’t lend themselves to this type of compaction.
Based on increased storage capacity, multiple foundation options and optimal storage conditions, cement companies ought to consider domes when selecting new storage facilities, Hardy said.
“A dome is a more economical structure for larger amounts of storage than other structures, and it’s more versatile than other means,” he said.
Editor’s note: This is an excerpt from an article published in the May 2017 issue of International Cement Review. To subscribe and read the full text, visit the ICR website.
By Rebecca Long Pyper for Dome Technology